Preventing VFD/AC Drive-Induced Electrical Damage to AC Motor Bearings
The use of variable frequency drives (VFDs) to control AC motors has increased dramatically in recent years. In addition to their low operating cost and high performance, they save energy. Today, the challenge facing system designers and engineers is to minimize damage to AC motors from bearing current. From its first minute of operation, a VFD induces destructive voltages that build up on the motor shaft until they find discharge paths to the frame (and then to ground).
In most cases, the motor bearings present the path of least resistance. Once voltage is sufficient to overcome the resistance of the oil film layer in the bearing, shaft voltage discharges, causing electrical discharge machining (EDM) pits — fusion craters in the race wall and ball bearings. This phenomenon continues until the bearings become so severely pitted that fluting, excessive noise, and failure occur.
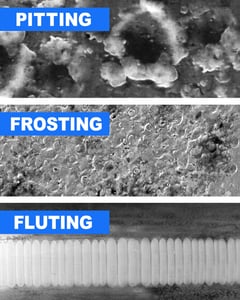
Over the years, researchers have proposed many solutions to minimize this damage and prevent premature failure. These range from blocking current flow with bearing insulation, to allowing current to flow without arcing by using conductive grease, to diverting the current by grounding the shaft. No one method is perfect for all motors, in all situations.
The shaft grounding ring is one of the newer and more effective methods. Like older carbon grounding brushes, they provide a low-resistance path from shaft to ground, so current flows through the brush, not the bearings. But shaft grounding rings have several advantages over grounding brushes and other methods of bearing protection.
Read the New White Paper